How they are
manufactured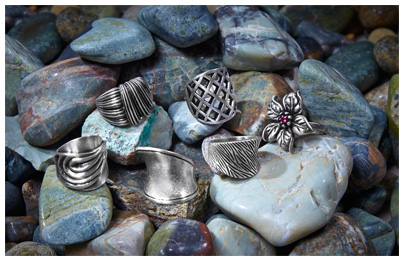
The rings are manufactured exactly
like fine jewelry.
In fact, most of the rings we
manufacture are copied from the real thing. The process
used is a casting process called “lost wax”. Briefly, a
model is made from wax which is enclosed in a
plaster-like substance. The wax is then melted, leaving
an exact space or mold duplicating the model. Then
molten brass is poured into every crevice of the mold
creating the ring. The stones are then set into the ring
and electroplated with 14K gold, or in the case of a
silver-tone ring, rhodium. After a final polishing
process, the rings are ready for sale.
We use only the best materials in the
manufacturing of our rings.
All
of our rings are made from brass as the base metal and
are electroplated with a minimum of 20 mils of 14K gold
or rhodium. Other companies use a lot of white metal as
the base metal in both rings and other types of jewelry.
For earrings and pins this is not as critical, but in
rings it makes a tremendous difference. Rings made from
white metal will feel light for their size, will bend
and break and the prongs will not hold the stones. Also,
white metal is porous and does not polish as well. White
metal is cheaper than brass, so a lot of manufacturers
are starting to use it in rings, especially those styles
that are not hand set. They may look OK, but they will
not wear well and if the stones are hand set, they will
soon fall out.
We
use only the highest quality of stones.
Over 75% of our stones are cubic zirconia. Other stones
used are simulated pearls, genuine onyx, opal, tiger
eye, abalone and Mother of Pearl, Swarovski crystal or
the highest quality spinels.
We use hand set stones in every ring possible.
This
means just what it says, each stone is handset into the
ring with prongs (another term for this is “prong-set”).
If you look closely, you can see that where there are
prongs, the stones are handset. Cubic zirconia stones
should always be handset as they are not foil backed,
will not hold well with glue and you would see the glue
through the stone. Even many of our pave looks are done
in a version of handsetting called “nicking”, where
cubic zirconias are handset using tiny beads at the
edges instead of true prongs.
We use a lot of two tone plating.
Two
tone plating generally has gold electroplate on the body
of the ring and rhodium on the prongs or in areas of the
ring to highlight the clear stones. Sometimes we use two
tone plating in the reverse to make a contemporary
statement. There are two additional steps in the plating
process, where there is a primer hand applied to each
area that will be rhodium plated, the ring is then gold
electroplated, the primer removed and then the area is
plated with rhodium. Many companies do not do this as it
is a more expensive process with all the hand work, but
it enhances the stones where it is used.
All rings are polished inside and out, smoothing out the
rough edges. In our rings, the inside looks as good as
the outside. |